Laser Welding Machine
Laser welding basics
Laser welding uses a highly concentrated beam of light on a very tiny spot so that the area under the laser beam absorbs the light and becomes highly energetic. As powerful laser beams are used, the electrons in the area get excited to a point where the material melts as the result of the atoms breaking the bonds with each other.
Laser welding process
Depending on the intensity of the laser radiation, laser welding is categorized as heat conduction welding or deep welding(keyhole welding).
Heat conduction welding
In this laser welding process, the energy coupled into the workpiece solely through heat conduction. The heat conductivity of the material limits the maximum weld depth. The welding depth for this process is generally lower than 2 mm.
Thus, heat conduction welding is used mostly to join parts with thin walls. The laser beam melts the mating parts along a common joint. The molten materials flow together and solidify to form the weld. The laser produces a smooth, rounded seam that does not require any extra grinding or finishing.
Applications are corner welds on the visible surfaces of device housings. Other applications can be found in electronics.
During this process, the laser beam melts the material and also creates a deep keyhole with approximately 1.5 times the diameter of the laser beam. This keyhole created by the laser welding process is surrounded by the melt.
As the laser beam advances along the weld joint, the keyhole moves with it through the workpiece. The molten metal flows around the keyhole and solidifies at the rare.
Welding depths of up to 25 mm can be realized for steel. The weld depth may be 10 times larger than the weld width.
This process is characterized by high efficiency and high welding speeds. This process is used in applications requiring deeper welds or where several layers of material have to be welded simultaneously.
Each of these welding processes have multiple practical uses within the manufacturing industry. In the hands of the right professional, the technology can help create customized pieces for various applications.
Continuous laser or pulsed laser for metal welding?
Different kinds of joints require different operation modes of the laser device.
Your laser welding machine can be equipped with one of the following two types of lasers: a pulsed wave laser or a continuous wave laser. The choice of one over the other depends on the thickness of the material you want to weld. Fiber lasers are available with both type of energy delivery.
Continuous wave mode
As the name states, the Continuous Wave (CW) lasers deliver a continuous, uninterrupted output. This output can have an upslope (soft-start) when switched on, an energy modulation while active, and a downslope when switched off (crater filler). Of course, this type of laser can also be switched on and off to create pulses. However, the maximum power level can never exceed the average power.
Pulsing wave mode
In contrast, the Pulsed Fiber lasers deliver a pulse of energy which is typically ten to twenty times higher than their average power. For example, a laser can have 300 W average power and 6000 W peak power. These lasers are often referred to as Quasi Continuous Wave (QCW) Fiber Lasers.
In pulsed mode, the gain medium is pumped in bursts to generate short laser pulses. Power, duration and frequency of the laser pulses are important parameters for material processing.
Why choose a laser welding machine?
Laser welding holds a number of advantages, depending on the needs of your application.
Laser welding is suitable for applications that require high speeds and for thin welding with low thermal distortion
It can realize spot welding, butt welding, overlap welding, sealing welding, etc., with a high aspect ratio, small weld width, small heat affected zone, small deformation, and fast welding speed; the weld is smooth and beautiful, no need to be processed or simply processed after welding, the quality of the weld is high; it is controllable, small focus spot, high positioning accuracy, easy to realize automation.
Benefits of Fiber Laser Welding Technology and its Applications
In a fiber laser, the laser light is generated in an active fiber and guided to the work piece by means of a flexible delivery fiber, which acts as a “light guide”.
Previous generations of laser sources, including rod-based Nd:YAG (pulsed and continuous wave) and CO2 lasers, were limited in their welding applications because of their wavelength, low average power or limited response to high-speed controls.
All of this changed with the advent of high-power continuous wave and quasi-continuous wave fiber lasers with a near infrared wavelength and ability to control with high speed and high resolution. Fiber laser system manufacturers, thus, have developed new hardware that makes new product applications possible.
Fiber transmission laser welding machine is a kind of laser welding equipment where the laser is transmitted through the optical fiber, collimated by the collimating lens into parallel light, and then focused on the work piece by focusing lens.
Another development is the multipurpose fiber laser system. Today’s laser machines are more flexible than those of the past. It is now common for these systems to perform multiple laser operations, including cutting, welding, drilling and marking, using one machine on a single part or family of parts.
Because process control is more precise, the range of process parameters is wider. The additional control provides even greater capability to laser weld dissimilar materials.
Benefits of fiber laser welding
From a practical standpoint, the use of beam delivery fiber expands integration options and facilitates the use of the laser in the manufacturing environment. Also, the high reliability, excellent uptime and favorable cost of ownership characteristics.
Fiber laser technology allow users to easily weld 0,05mm (.002”) away from the most complicated and intricate component parts without damaging heat sensitive materials.
Fiber laser welding machines have proven to be a highly successful investment for a number of manufacturers, reducing post finishing processes and cycle times while creating productivity and return on investment (ROI).
The inherently high speed of laser processing combined with the ease of high-speed automation and elimination of most post-processing steps provide significantly shorter cycle times than competing technologies. MORN LASER fiber laser welding machines deliver more good parts faster than alternate joining techniques.
Welding with fiber laser
Fiber laser welding machines have greater flexibility for non-contact long-distance welding of hard-to-access parts.
You can separate the laser beam by time and energy, or process multiple beams at the same time, and realize multi-station processing, which provides conditions for more precise welding.
The optical fiber transmission laser welding machine has the advantages of good beam quality, fine light spot and flexible installation. It is suitable for welding optical fiber connectors, microelectronic components, medical equipment, precision parts, etc.
Laser welding is usually done without filler metals so parts need to have good fit with a gap that’s less than 15% of the thickness of the thinnest component, which limits its scope of use. The use of wire-filled laser welding can greatly reduce the limitations for welding gap. For example, for an aluminum alloy plate with a thickness of 2mm, if no welding wire is used, the sheet gap must be zero to obtain a good weld shape. If a φ1.6mm welding wire is used as a supplementary metal, even if the gap is increased to 1.0mm, the weld can be ensured. In addition, filler welding can also roughly adjust the chemical identity or perform multi-layer welding of thick plates.
Laser Welding Machine For Sale
Experience the MORN LASER 4th handheld fiber laser welder in action, spot welding, wobble welding, filler welding, large object remote laser welding, hard-to-access parts laser welding etc
To THE PRODUCT
This laser welding machine offers a turnkey solution for automated laser welding. Suitable for welding circular welds of stainless steel, carbon steel and other workpieces.
To THE PRODUCT
One system – countless benefits. Enjoy both manual laser welding and auto laser welding with one machine.
This large format custom laser welding machine can be tailored to your exact requirements. Thanks to its larger working area, much bigger parts can be processed.
Laser Power and Cutting Thickness
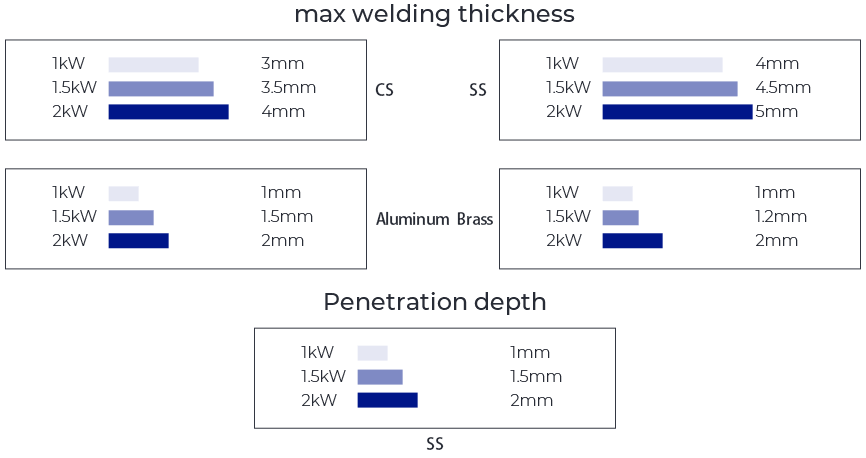
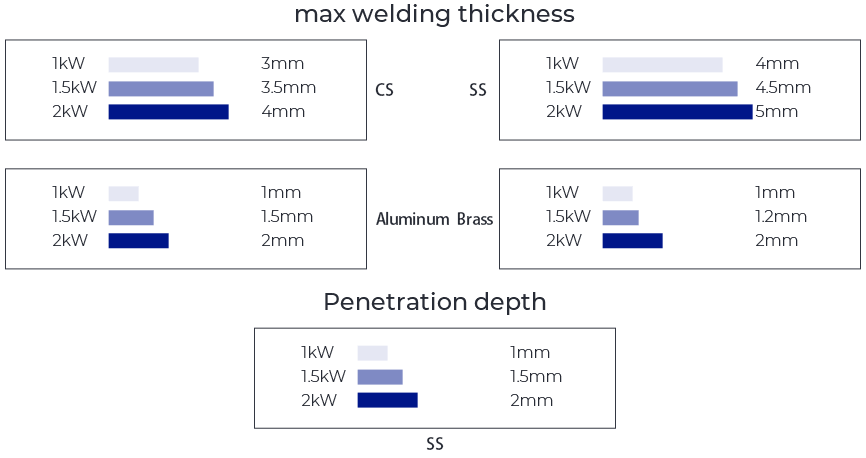
Laser Welding Videos
This video displays the welding process of our big size auto laser welding machine. Maximum welding size 1m, maximum thickness 3mm.
This video displays the welding process of 2.0mm Aluminum welding with MORN LASER 1500W Laser Welding Machine. Cost-effective, it has been favored by many customers. Customized solutions are available.
This video displays the welding process of 1.6 mm Aluminum welding with MORN LASER 1500W Laser Welding Machine. Cost-effective, it has been favored by many customers. Customized solutions are available.
This video displays the welding process of MORN LASER 2000W Auto laser Welding Machine. What’s more, you can enjoy the visual welding process in it. Buy one right now and seize the market opportunity.
MORN 1000W Fiber laser welding machine for carbon steel video
MORN 1000W Fiber laser welding machine for 1mm stainless steel video
This video displays the welding process of MORN auto laser welding machine for brass, ss, and new energy aluminum battery.
This video displays the working process of our 2000W automated laser welding machine.
Laser Welding Machine Applications
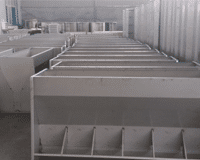
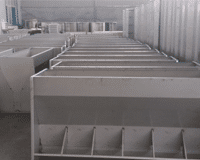
Laser welding pig farm breeding equipment
Carbon Steel laser cutting in different thickness
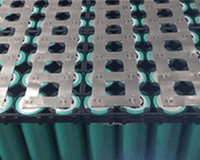
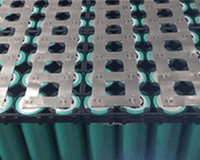
Laser Cut Stainless Steel Sample by Sheet Metal Laser Cutting Machine
Stainless Steel laser cutting in different thickness